For those that don’t know, the fabric industry is moving more and more to using digital printing for printed patterned fabrics. Recently we have gotten questions about digital printing in general, and how it differs from traditional printed fabrics.
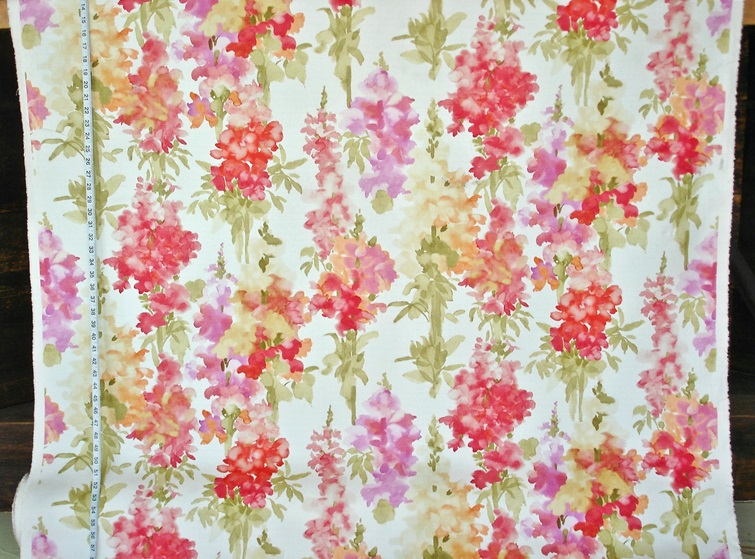
Fabric printing with digital printers started in the late ’60’s. Remember when people took photos and printed them onto fabric for various home projects? Digitally printed home decorating fabric uses the same idea. But, the printers and inks have changed over time.
So, digitally printed fabrics are just that… fabrics that are printed by a digital process, like printing something on paper using your computer and a printer. Older textile printing methods, which companies still use, are block printing, screen printing, and rotary printing. While older methods use dyes, digital printing is done with inks that are dispersed from ink jet heads. What is ink? Ink is a colorant made up of very small particles suspended in a liquid; dye is dissolved in a liquid, it is a solution. All methods of printing textiles have their pros and cons.
For digitally printed textiles a large printer, wide enough for fabric to pass through, is used. A digital file of the art work to be printed is programed into a computer that runs the printer. The inks colors needed are also programed into the computer, which tells the printer what color, and how many drops of ink to use, and while the digital file of artwork tells the printer where the color should go.
There are two types of digital textile printers, single pass printers and a multi pass printers. They have very small jet heads that disperse the ink. The multi pass printer goes back and forth over the fabric, and then the fabric is moved a specific amount. The single pass printer has the fabric moving, as if it were a conveyer belt, under the ink heads.
There are basically four different kinds of ink used for textile printing: acid, reactive, subliminal, and pigment inks. The ground cloth used, and the colors and saturation needed, will determine what inks are used. Each ink is best used on certain fibers, just as for dyes. So, for instance, if a 100% cotton fabric is used as the ground cloth one would use pigment or reactive inks.
The ink is dispersed in small droplets. In the past there have been issues with the ink jet heads clogging. The ink has to be able to go through the ink jet heads without clogging; the ink needs to be appropriate for the printer and the heads, as well as the fiber being dyed. The size and height of the ink jet heads from the fabric are also a consideration as they determine the dispersion and spread of the droplets, which effects the final look of the pattern. The saturation and brightness of the colors are influenced not only by the type of ink and fabric used, but are also effected by the finishing of it.
There are two ways to transfer the art work to the fabric. One is called subliminal digital printing, and one is direct printing. The subliminal printing uses a heat transfer method, where the design is printed onto a paper with subliminal inks. This is transferred to fabric using high heat and pressure, which changes the ink from a liquid to a gas, which penetrates the fabric. Once cooled, the colors are locked in the fabric. This is done on polyester. The direct method is similar to using a printer to print out a design with a home printer, where the ink goes directly onto the fabric.
When digitally printed fabrics first came out they were extremely expensive. Few companies were doing full width home decorating fabric printing; I am talking world wide. The normal American width is around 54″ wide, in Europe it is often wider. The printers were, and still are, extremely expensive. I know one company that decided to start their own digital print division, so the printing could be done in house to save money. They abandoned the idea as they came to realize that printers were constantly needing upgrades, and often needed to be exchanged for ones, as the technology changed. So, what happened is actually the same as what happened with traditionally dyed fabrics. The companies have farmed out the printing to digital print companies, just as they do for traditional dye printing methods.
And this is where things become more complex. Unlike other fabric, home dec fabric has to meet certain standards for use. Just as with traditional print methods, fabrics that have been digitally printed need to conform to industry standards. While a company may want a certain look for a pattern, that fabric has to stand up to the use it was intended for, as well as meet industry standards.
Some things in the textile printing process have not changed. Just as with traditional dying methods, the fabric needs to be pre-treated before it is printed. And, depending on the inks used, it may need to be finished.
When digitally printed fabrics were first available to us, many of the mills gave a choice of fabrics from which to chose for any given pattern. One fabric company gave a choice of fourteen different fabrics to use.
This has changed. What we now see is not a full range of fabrics that can be digitally printed, but what a fabric company offers, which is based on what a printing company uses. Rather than a full range of ground clothes that can be used, we are given a choice of what the printing company uses. Most only use one or two different ground cloths, which are offered to the fabric company. So, if a company wants a specific ground cloth they go to the print company that offers it.
In a way, things have come full circle. For, this is exactly the same process that fabric company and mills have used with traditional printing methods. The companies have in the past used specific mills that used specific ground cloths for the printing. For instance P.Kaufmann’s County Fair is printed on the original ground cloth specified by that company. And, that ground cloth is available from a specific printing mill. So, the pattern is printed at the mill that has that ground cloth.
Rather than going to a single printing company and choosing from a wide selection of ground clothes, a fabric company goes to a printing company that offers the ground cloth they want to use. If a specific heavy fabric is needed they go to the printing company that offers it, and if they wanted a light weight version of the same pattern, they might use another print company. One might be printed in Europe the other in the far east.
This saves the fabric company, the printing mill, and the buyer money as it saves on the set up, as they are not switching out different cloths and ink all the time.
When we first were offered digitally printed fabric it was confusing, to say the least. Imagine being given fourteen different ground cloths to chose from for a fabric design. And, it was extremely expensive. There was a learning curve for the fabric companies, the printing companies, and for us. We all suffered with the growing pains of this new method.
For us it seemed as if every time we would order a specific print, the ground cloth would change, or the ink colors would change as they had moved from one ground cloth which required one type of ink to a new ground cloth that needed a different type of ink. This was frustrating, not just for us, but for the companies as well. Things have settled down a bit. But, we still run into things.
The Scandi bird fabric is a case in point.
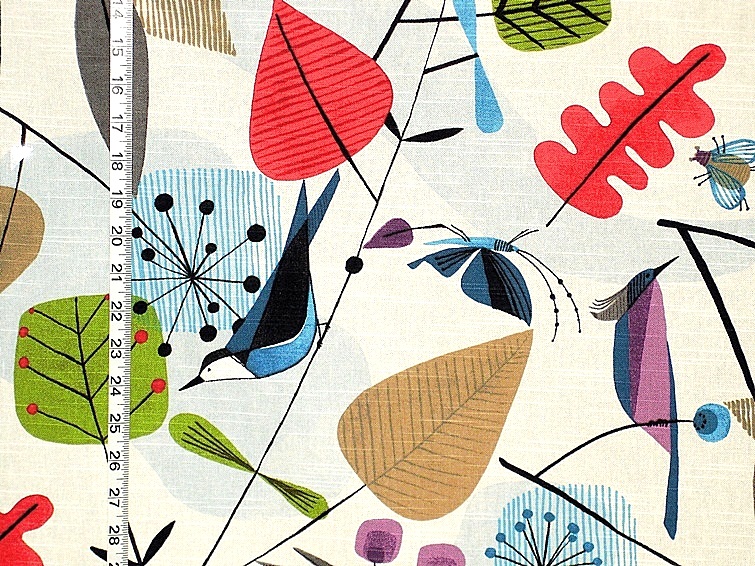
The original had a rotary printed pattern that was printed on a cotton/polyester fabric, which was woven with a slub. When the pattern was discontinued, we wanted to run it, as it had always been. But, the original ground cloth was no longer available. So, first they did it as a screen print on a new cloth, which we did not like as we felt it was too light weight for home dec use. Then the company did not want to run it as a screen print at all. So, they sent us samples of it done digitally, on their new ground cloth, which was still too light. And, the colors were not the same as the old. The red, especially was way too brown.
We sent back the information of what we needed them to tweak. This went back and forth- as we worked out colors, saturation, etc. We finally approved one. But, I would not accept the new ground cloth… we were at an impasse. Now, there was an older ground cloth, not the original, but one which we had used in the past, which it turned out, was still available. But, the printing company would only run it on that ground cloth if enough other patterns were run at the same time, as they did not want to change out the cloth and ink. So, we either had to run enough yardage or patterns to meet what they would do as a minimum, or wait for another company to also want to run something using that same ground cloth.
This is actually not anything new, as all mills have minimums for printing as the set up costs are high. But, one of the things touted by ink print companies is the ability to do short runs for people, which they have since scaled back, at least for the home dec textile industry.
We finally did get the Scandi bird printed digitally, on the fabric we approved. But, this took well over a year to get to our specs.
The same thing happened with the Venice fabric. The company that originally had the pattern dropped it. And then that company sold the business. The rights to the Venice fabric moved to the company that bought the original company, but they did not want to carry it. If we wanted it, we had to run it. The original screens had been destroyed, so it had to be digitally printed. From the first inquiry about running it, getting and approving samples, and then actually getting the fabric took over a year.
The blue aqua coral fabric is also printed on a specific ground cloth that we like. The company wanted to keep it on the new ground cloth, as they could run the printer, continuously, just changing out the digital artwork and the colors needed. But, again, we wanted a different ground cloth, which we eventually got.
Digitally printed fabrics do not match the original screen printed fabrics. The colors are different. The difference between the inks and dyes, the different methods of delivery for the colors, the saturation, the actual fabric, and finishing, as well as other factors all influence the colors and tones.
One interesting this is there is no limit to the size of a repeats with digital printing. One can have any size of vertical repeat one wants. With rotary printing, the repeat is limited by the circumference of the screen. With flat bed screen printing the repeat is not limited, but flat screen printing is a whole different cup of tea. It takes up a large amount of space, and is difficult to do well, and is time consuming. We have had hand prints with repeats of 8o inches, using 26 different colors. While this is a difficult thing to do well with flat screens, with a digital printer it would be quite easy.
Now, people have the misconception that digital printing means that there aren’t any variations between the runs. That is just not so. We have had color variations. And we once got in a fabric where the whole pattern had been totally scrambled. It looked kind of neat, but was not what it was supposed to be.
The above was the pattern as it should be.
Below is what once came in.
WHY DIGITAL PRINTING
So, why digital printing? From the mill’s point of view, it makes sense. It is cheaper.
One has a digital file, and that can be easily stored. With rotary printing the screens have to be cut, one for each color used. And, they are expensive. With between fifteen to twenty four screens used, the company has a sizeable investment just in the screens. And, they need to be carefully stored so they don’t get damaged, which takes up a lot of space.
There is virtually no set up with digital printing. With rotary printing colors need to be chosen, and cloth set up, and someone has to over-see the printing process. And, then to change to a different colorway, the screens have to be washed and the new dyes mixed. The run for screen printing is usually between 1200 yards and 4500 yards. And then that amount of fabric has to be finished, rolled, transported, and stored. And, a company has no idea how well a pattern will move. Will it sell?
With digital printing one can set up the computer with the design, change colorways easily, and push a button. And one can print virtually on demand- from a yard to whatever length is needed, it can be done. While a digital printing company can do a yard at a time, most have a minimum of 350 – 400 yds, versus 1200 yds for a rotary printed fabric.
With digital printing a fabric company can cut down on every single cost of producing a fabric, from set up, space, transportation costs, man power. And, one does not have the sizeable investment that can go down the drain if a fabric does not move well.
So, what is the actual difference to you, as a person, buying a digitally printed fabric.
I think the biggest difference is in the ground clothes being used by companies for the printing. This is an actual choice made by the company. We are seeing mostly 100% polyester and 100% cottons. Blends are not used as much. It may be thinner than a fabric that would have been used in the past, though one company only uses one quite a lot heavier than they used to, and another gives a choice of very heavy or very light.
If a company is moving a pattern from a screen print to digital printing the art work is the same. The companies do not rescale the art work, the patterns and repeat will be the same as the original. The main differences we see are in the ground cloth, which influences the hand of a fabric, and the coloring, as ink colors and dyes are not the same. They can be close in color, but they will not be a match.
I think it is best to think of the digital fabrics using an older fabric design, as a totally new fabric, rather than trying to hope it will be the same as the older version of it.
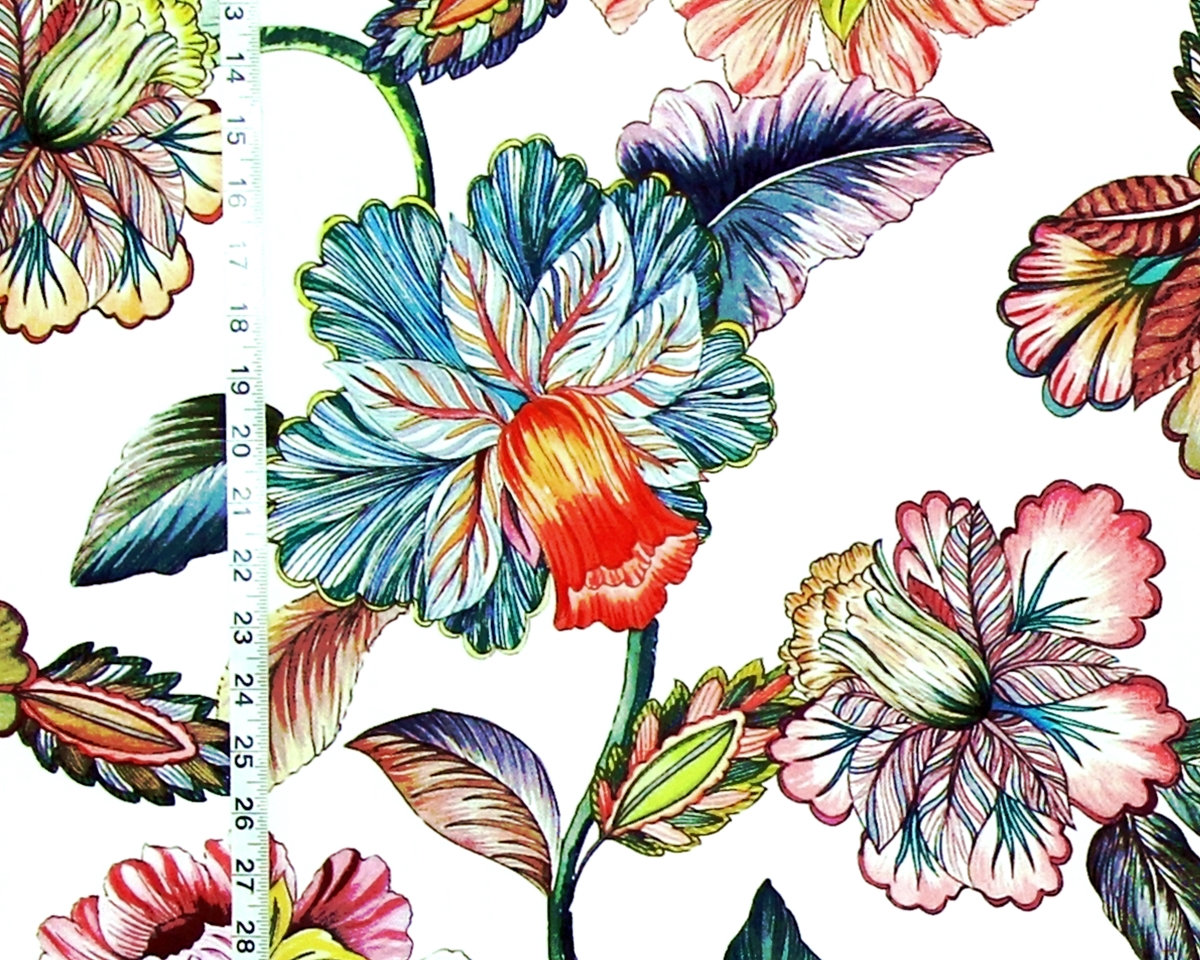
If one looks at the floral fabric above, which is digitally printed, one can see how precise digital printing can be, with the very fine lines used, as well as how the colors can be layered to get different color tones.
This is not to say older print methods can not achieve the same precision or soft look. They can. But, it is more costly to do it and takes more skill to achieve. With a screen print each color would need its own screen. Even if there was a light and dark color of the same tone used, each tone needs its own screen. With the digital print that is controlled not only by the color used, but also by dispersal of the ink- how many dots were used in a specific area.
The home decorating businesses will be utilizing digital printing more and more. I know one company that had 100% of their prints done digitally this year. As the technology advances both in printers, inks, and methods there will be fewer companies using rotary printing, and even fewer using screen printing. This is a new age of textiles.
_______________________________
SOURCES
https://www.fespa.com/en/news-media/features/colour-management-in-digital-textile-printing
https://imieurope.com/inkjet-blog/2016/2/9/selecting-the-right-ink-and-process-for-digital-textile-printing-part-1-ink-types
https://www.hollyflower.com/digital-printing-on-fabric
https://blog.spgprints.com/fabric-textile-printing-techniques
https://blog.spgprints.com/what-is-digital-textile-printing
https://www.globalimaginginc.com/blogs/